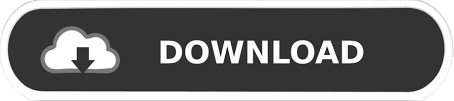
Setting the start point to optimized or random position results in zits spread all over the print. Start Points determines, where the layer start seam is positioned. Use Variable settings wizard to split the process (see below). We’re using 2 perimeter setting for first few millimetres of print to improve heatbed adhesion and reinforce the bottom part to fight warping caused by heatbed temperature. If you experience layer start under extrusion, setting the layer height to 0,2 mm slows down the extrusion and helps to correct this. The layer height is usually set to 0,25 mm for the best speed/quality ratio. This tab contains all the settings determining the number of perimeters, layer starting point – seam and possibly number of bottom/top layers if necessary (control surfaces horns, steep overhangs, Pawnee’s face, etc…). Set the values according to the image for a general single wall part. Turn off the Coasting and Wiping as they have little to no effect, but keep the Extra Restart Distance to compensate oozing. If you’re going to print from foaming material, such as LW-PLA, set the Extrusion multiplier around 0,5 and set the Retraction Distance to 0. These values require some tweaking, but once you find the right settings, you just use the same values for any factory file in the future. If you experience under extrusion after travel move of the head, there is Extra restart distance to prime the nozzle before starting a print move. Setting the retraction distance too high could result in clogged hotend. In general, if you experience stringing, raise the Retraction distance in steps of 0,2 mm until the stringing stops. For Bowden extruders (extruder stepper is not part of the print head and the filament is being fed through a long Bowden) the Retraction distance should be in between 4 – 8 mm. For direct-drive extruders (hobbed bolt right above the hotend, the stepper motor is part of the X carriage) the Retraction distance value should be about 0,8 – 1,5 mm. The Extruder tab also contains all the necessary Ooze control settings. Calculate the extrusion multiplier as a difference between resulting and suggested weights. The tolerance should be within a few grams. Print the test part (the bigger the better), check the weight and compare the resulting weight to the diagram.
#3dlabprint cfd pdf#
You can find suggested weights of most parts in the PDF user guides of each plane. We need to make the part lightweight yet strong enough. The Extrusion multiplier is a value where you can adjust the overall weight of printed parts. 1,75 mm and 3 mm are just the systems, and the actual diameter value may vary a bit causing under extrusion or over extrusion. Please measure the average filament diameter of each spool with callipers prior to altering these settings, we’ll address this later on the “Other” tab. This tab contains all the necessary settings to tune up the extrusion and retractions. Set the values according to the image as a starting point. Let’s start with configuring the basic process for the wing/fuselage part. Direct drive E3D V6 hotend seems to be a perfect choice.įurther in this article, we’ll try to explain the aspects of preparing the gcodes from scratch, so you better understand all the settings. Also, keep your hotend in a good shape, and if you’re still unable to tune up the extrusion, consider upgrading it. Check all the axes could move freely and are perfectly perpendicular to each other. Please note, any Simplif圓D settings couldn’t fix a poorly built or designed printer. If your printer requires tweaking the settings, use the factory file as a starting point and adjust only the necessary parameters. If you’re using original Prusa i3 compatible printer with direct drive extruder, all you have to do is open the factory file, hit Prepare to print button and save the resulting gcode to your printer SD card (or just use our prepared gcodes, made precisely this way). Since we provide factory files for all parts, all of the necessary work, such as setting up processes and bed layout has been done for you.
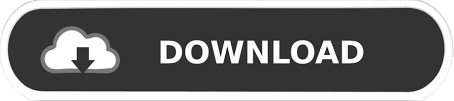